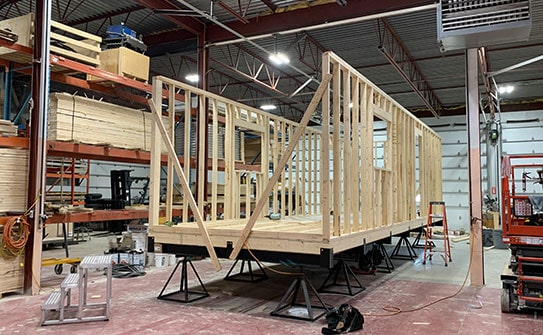
As a society, we love to customize. Whether it’s our car, our home, or even our take-out order, we like to make things in our lives unique to us.
The same goes for our modular buildings. You might think that all modular buildings are the same, but that’s not the case. You can customize them like you would a traditionally built structure.
We’ll walk you through the process of how to customize a modular building and provide some tips for customizing your modular building.
Why Should You Design a Custom Modular Building
There are many benefits associated with modular construction methods. If you need a custom-built structure and you’re deciding whether to go with traditional or modular construction, there are several reasons to look into modular building and customization, including:
Speed of construction
Safety
Labour force accessibility
Avoiding/limiting weather delays
Less site disturbance
Less disturbance to neighbours or people on site
Fewer deliveries
Cost savings related to the speed of construction
Any one of the preceding reasons is an advantage to creating a custom building, but all of them together show why modular construction has become increasingly popular over the years.
What Should You Consider Before You Start Customizing
Before you start building your custom modular building, the first thing to consider is your budget. BOXX custom buildings are only purchased; they can’t be leased like our standard fleet buildings. However, banks will finance a modular building when you do custom construction.
You also need to think of your timeline/schedule and how that can fit in with the modular building process. Knowing how much time you have and when you want your building to be operational can help you decide what customizations will work within your timeline and which ones you need to adjust.
The next item to consider is how much square footage your building footprint can accommodate. You don’t want to design a custom modular building and find out it won’t fit once it’s delivered. You will also need to consider who will be accessing your building (i.e. customers, employees, and the general public) and how much space you need for parking on your site. Also, check your site’s proximity to other buildings/structures. You need to have space around your building for the delivery and installation of the modules.
Another area to check is your proximity to utilities, like electric or gas, water, and sewer. If they aren’t available, having to run new lines or extend current ones will cost a great deal of money, and doing this also comes with the risk of encountering underground obstructions which can cause serious delays to your timeline.
This is where understanding the zoning and permitting process comes into consideration. You need to see if you can even put a modular building on the site and what your site plan calls for. This is also when you should check your occupancy requirements.
Doing so can also help determine how much space you need and if you need any specific accommodations. You also need to check the accessibility of the building and if you need to make any adjustments to things like door width, washrooms, and entrances (i.e. ramps vs. stairs)
Another area you need to consider is your building’s layout. You need to determine what spaces you need, such as offices, labs, kitchens, washrooms, or lockers. This also helps you determine the number of doors and windows you need as well as their size and location.
You’ll also need to consider environmental awareness— are you building in wetlands? Is there sufficient stormwater runoff/drainage around your building? Is the soil on site compact enough to place a building on top, or does it need work?
Once you’ve determined your site is safe to build on, you need to develop it. This can include things like:
parking/striping
street access
curbing
landscaping
paving
lighting
gates
signage
security requirements
This can involve some excavation and grading, which is where your engineer comes in to help.
One of the best parts of a custom building is picking your internal and external finishes. It’s important to identify any specific materials required for the building that may have a long lead time and ensure they are ordered with enough time to align with your building schedule. And if there are special architectural requirements, you’ll need to engage an architect along with your modular building dealer.
What are the Steps in Creating Custom Modular Buildings?
Custom modular buildings don’t just appear out of nowhere. They take planning and generally follow the process described below.
1. Design and Engineering Phase
In this phase, you might be consulting an architect along with BOXX sales and engineers to start the modular process. This is when you begin to go over your customization options for modular buildings and we can help you through the decision-making process.
2. Permitting Process
This step deals with the legalities of the modular building process. You’ll be responsible for getting any necessary permits and checking zoning regulations in your area. A good place to start is at your local zoning office.
3. Building Fabrication
This is when your building is being built. Unlike traditional construction, this takes place in an off-site facility. The builders will add your customizations along with any standard features. Modular construction is quicker than traditional building partly because it takes place at the same time as excavation and grading.
4. Excavation and Grading
This takes place at your building site. Sometimes your site isn’t set up for a building, so you will need to make the ground level or remove old pavement or trees. This is also when you would run utilities, underground water lines, and sewer lines. You might be able to skip this step if your site is already prepped for a building or it might take minimal time and work to get ready.
5. Foundation Installation
If you choose a building that requires a foundation or you want to add one, this is when you would do that. However, if the type of building you choose doesn’t need a foundation then you can skip this step.
6. Building Delivery
Once your building is done and the foundation is in, the next step is delivery of your building from the manufacturer. One of the benefits of a BOXX building is that your building is manufactured in sections and assembled at your delivery site so it’s easier to transport.
7. Building Installation
Installation is the last step of the process. This not only includes installation, but it’s also the punch list, closeout, and occupancy.
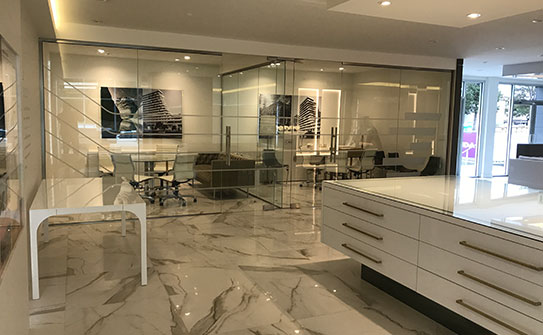
BOXX Customization Options
At BOXX we believe you should have a building that fits all of your needs and works exactly how you want. Our modular experts can help you make the right decisions for your business in a variety of areas.
Structure
One of the most important decisions to make is what material(s) you want to use for the structure of your building. There are several options you can choose from like:
Steel and concrete
Wood frame
Hybrid (wood with steel studs)
Each one has its pros and cons, and doing your research with an expert will help you pick the right option for you.
Floorplans
For custom buildings, you can create the floor plan to your exact specifications or you can look at our standard floor plans for reference if you need a starting point. Modular buildings are done in long rectangles so you need to consider where the modules split when designing a building.
This is why it’s important to bring in an architect early in the process, if one is necessary. Then they can work with our modular sales/engineering team to make sure the layout and design are aligned with how modular buildings work.
You also need to consider mechanical systems like HVAC. You can choose between a split system, RTUs (rooftop units) or end mount/BARD-type units. Split systems are installed onsite, RTUs generally need to be crane-set, which is expensive but more aesthetically pleasing whereas BARD units come with the building from the manufacturer. BARD and RTUs are ducted, while split systems are not—they’re one unit per room.
Walls
Any drywall should be installed onsite because it’s more delicate and can crack/shift in transit. Typically modular units use VCG (or Vinyl Covered Gypsum) for walls that can be repainted or replaced separately for easy maintenance.
Ceilings
Typically modular ceilings are made with acoustical tiles, also known as drop ceilings, but you can also have a hard ceiling, like drywall or textured. However, that would typically be installed on-site instead of at the manufacturer.
You’ll also need to think about ceiling height and the ductwork. You’ll need to keep enough room in the ceiling for the ductwork to fit. Another thing to remember about ceiling height is that ceilings above 8 feet will be more complicated for manufacturing and delivery.
Cabinets
Most people install cabinets in their modular buildings to use for storage. These cabinets can come custom from a manufacturer, or they can be acquired from a custom cabinet maker and installed on-site. This allows you to have the exact style, material, colour, or even the number of cabinets that you want.
Remember…
Similar to a site-built building, you can choose almost any materials you want. There aren’t limitations for material selections with a custom building.
But the more custom selections you make that are not installed at the manufacturer, the slower your build and move-in time will be. If you use typical modular materials, your building can come to the site up to 90% complete. But if there are custom cabinets, floors, or finishes they will need to be done on-site.
Tips for Customizing Your Modular Building
Consider getting an architect early in the design process. Make sure that the architect is aware you want to use modular and that they are familiar with modular. The right architect can help you see what customizations are possible for your building and let you know of any drawbacks or suggest improvements.
As soon as you decide you want a custom BOXX modular building, connect with our sales representatives. They can review the different building options and what would work best for you. They can also guide you through the entire process and give you advice.
Also remember even though it’s modular, this is still construction. It’s not the same as renting an office trailer—think of it more like a traditional stick build in many ways. While it’s a quicker process than traditional construction, it’s still going to take time and won’t be immediate. However, if you’re patient, you can have the perfect custom modular building for you and your business.
Have any questions on how to customize a modular building?
Contact our experienced sales team and they can help get you started on your custom modular journey.
Ready to solve your space needs?
Modular buildings are the way to go. Request a quote or contact us today to get the conversation started. We’d love to talk to you about how modular can meet — and exceed — your needs.